

Knock sensors rarely degrade they typically fail and will not produce a signal no matter how hard you hit them. But, this type of testing can be hard on an engine. The lean conditions might produce an engine knock. If the sensor is inaccessible, you can run the engine and pull the fuse for the fuel pump and let the engine stall. If the sensor is out in the open, you can use a blunt chisel and hammer and strike the area around the knock sensor. There are two schools of thought for testing. On V6 and V8 engines, the knock sensor might be in the valley of the engine under the intake manifold.
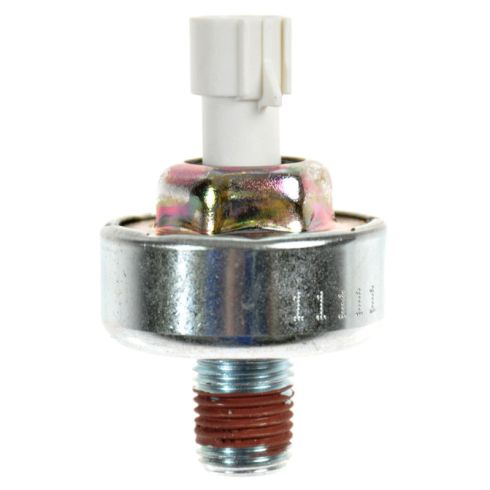
On an inline engine, the sensor is easy to access. Knock sensors are mounted on the block near the base of the cylinder head. If you are testing the sensor on the vehicle, you need to access the connector. If you are using a scope, make sure the AC filtering is turned off. If you’re using a meter, set it to AC volts. It can also identify if the event happened before or after top dead center. This way, the ECM can determine if the driver just hit a pothole, or if a knock occurred. The ECM looks at the crank angle sensor data to determine at which cylinder the event is taking place and whether the crankshaft had a sudden change in speed. The knock sensor is not the only sensor responsible for detecting engine knock.

The ECM can look at the output from the knock sensor and determine if something is going wrong in the combustion chamber and take action, like changing the ignition timing or adding fuel.
